How Construction Inventory Tracking Improves Resource Management and Cost Overruns?
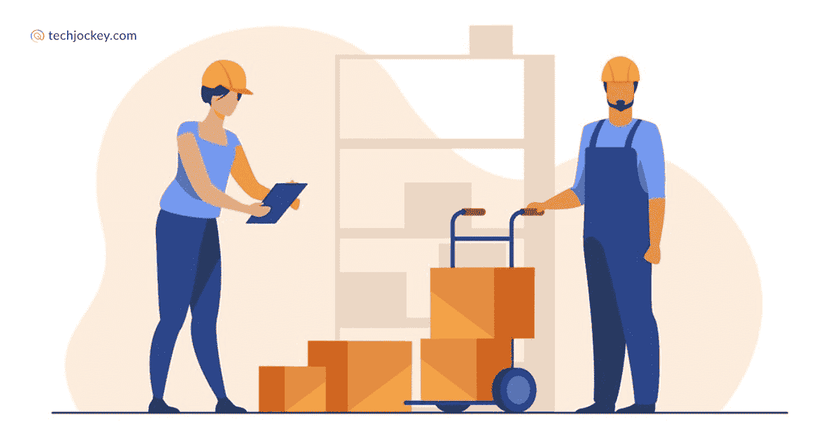
Inventory costs approximately 50-60% of the total project cost in the construction industry. Lowering these costs can result in enormous savings, even if it is just 5-10% less.
But what if these costs overrun?
This is a very common and the biggest issue that every construction industry faces. Going over budget can lead to lower profits, delayed timelines, and affect relationships with your clients. It makes it difficult for construction businesses to stay on track financially. Even the labor working on the project is of no use if the material is not available.
Thus, it becomes necessary to have proper construction inventory tracking. This strategic move can help businesses save money, reduce waste, and make better use of their resources.
This blog post will discuss everything about the impact of construction inventory tracking on resource management and cost overruns. Let’s start with how poor inventory management affects your business.
The Cost of Poor Inventory Management
If inventory is not managed properly at the construction sites, it could result in a loss of money. A few drawbacks of poor inventory management are discussed below.
- Delays in projects due to material shortages: If you miss construction inventory tracking from your workflow, there is are high chance of material shortage. And when materials are not available when needed, it could stop the construction work, pushing deadlines.
- Wastage due to overstocking: Materials can expire if you overstock them. Especially, if you have overstocked perishable or season-sensitive items like paints, coatings, adhesives, etc. This wastes both space and money.
- Lost or misplaced equipment: Without any centralized system to track inventory in large construction sites, tools and equipment can easily go missing. You will further require replacements, costing twice 2x money for the same material.
- Labor downtime due to missing resources: Workers with no work to do because of missing tools and materials could affect productivity and increase labor costs.
- Inaccurate budget forecasting = unpredictable expenses: Poor inventory oversight results in unexpected costs and unreliable budgets, making it difficult to plan future phases of a project.
- Lack of visibility across teams and sites: Without real-time visibility into inventory, site managers and procurement teams find it difficult to stay aligned. It increases the chances of duplicate orders leading to cost overruns.
Thus, construction inventory tracking is important to keep an eye on the ins and outs of every construction material.
What is Construction Inventory Tracking?
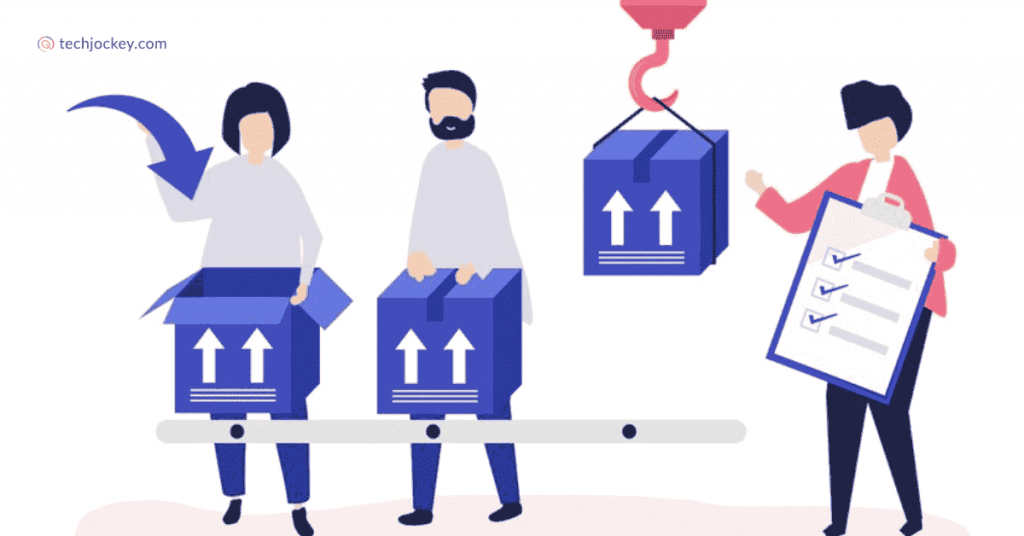
Construction inventory tracking is the process of managing and controlling inventory in real time. This is to ensure that every material and equipment is available when it is required, and helps avoid understocking and overstocking. It typically involves:
- Keeping detailed records of all assets
- Monitoring inventory levels from time to time to avoid delays
- Optimize resource allocation as per the material present
- Managing project timelines and budgets
Proper construction inventory tracking is very important to overcome all the challenges in the above section.
Inventory Tracking and Resource Management
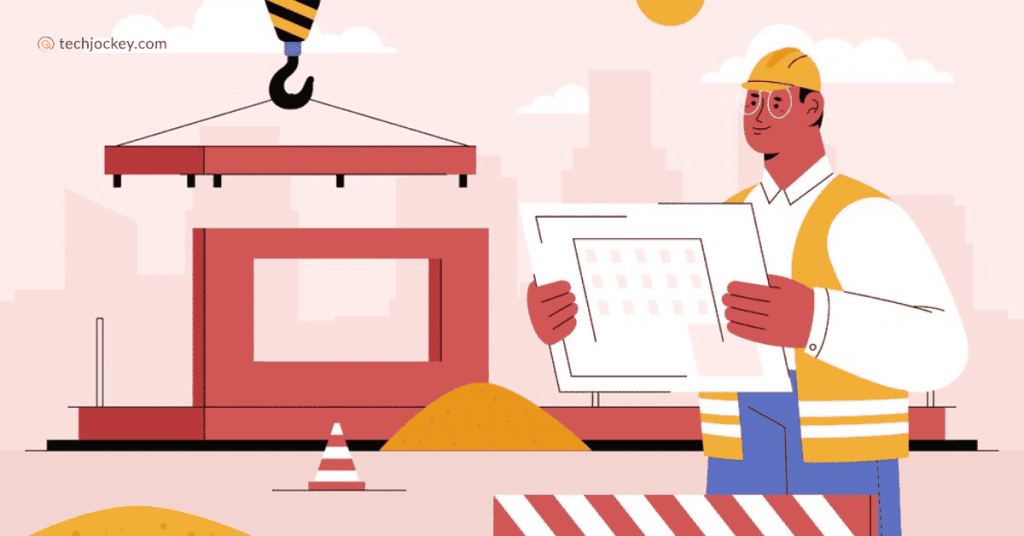
Every pipe, pallet, and power tool contributes to the bigger picture, but without proper oversight of these resources could lead to major disruptions. It makes it important for construction companies to efficiently track inventory and manage resources.
A large construction company has to look for multiple sites simultaneously. All the sites must be equipped with the resources required. If there is no clear system in place, project managers keep juggling multiple spreadsheets, or paper records to manage resources.
“You can’t manage what you can’t measure.” Peter Drucker
In construction, this means that you must streamline inventory tracking management to avoid any wastage or cost overruns.
Reducing Cost Overruns Through Inventory Visibility
Labor is the main asset for any construction project, and if the labor is idle due to missing resources, it can affect your budget.
Experts in the construction industry have found that there is around 20-30% labor downtime rate due to poor planning or unavailable inventory.
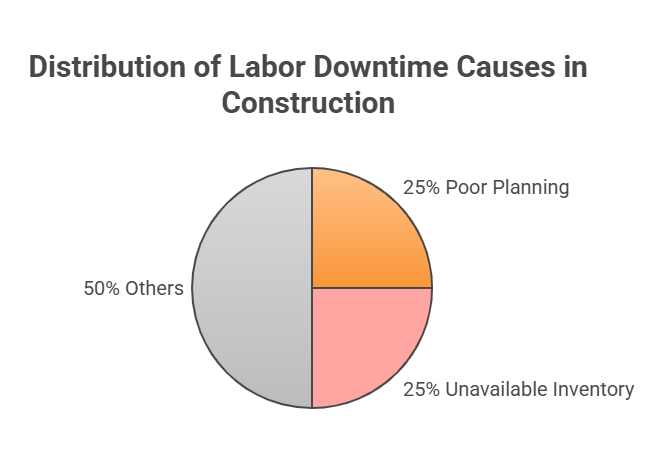
When site managers keep a proper eye on construction inventory tracking:
- They know that all the required materials are available, and it helps them to schedule labor more effectively.
- Accurate cost estimation can be done for future resources
- Proper insights can help them find any financial discrepancies that have come up before.
- Teams are less idle, and it helps reduce overtime labor costs.
Suggested Read: How to Use Construction Project Tracking Software Effectively in 2025 [Free Templates]
Challenges in Manual Construction Inventory Tracking
Manual inventory means no real-time visibility.
When site managers do not know which material is available and where they cannot effectively assign workers or allocate resources for a specific project.
There are a lot more challenges in manual construction inventory tracking. Here we go with the list:
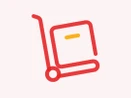
Zoho Inventory
Starting Price
₹ 1800.00 excl. GST
- Lost papers: Records and checklists are sometimes lost and do not reach to the supervisors. It delays the workforce deployment.
- Wrong data: There are chances of clashes between what material is recorded and what is actually available on-site. It hampers projects and sometimes results in client disputes.
- Resource theft: Missing or stolen materials can affect the timeline of critical tasks and also increase the cost of buying the material again.
- Siloed systems: HR, procurement, and site teams use different software for construction inventory tracking. It keeps everyone on a different track and results in misalignment between labor and resource availability.
The Role of Construction Inventory Tracking Software
For all the challenges discussed above, there is one solution: construction inventory tracking software. Reports say, “The global inventory management software market is expected to grow from USD 2.31 billion in 2024 to USD 4.79 billion by 2032.”
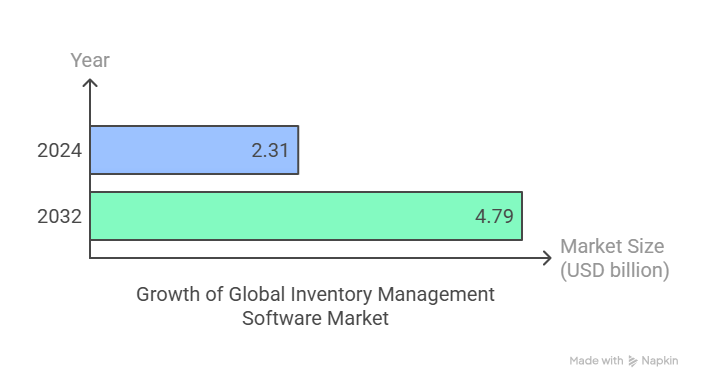
This shows that a wide number of companies are shifting toward managing their inventory with technology.
Construction inventory software helps the project-site staff in better inventory management. Below are a few benefits discussed:
- Site teams can easily check the real-time availability of the resources.
- A few software offers mobile accessibility to make the job of inventory tracking more easier. Teams can check stock even before they check in to the sites.
- Site managers are notified instantly when any material is running low.
- Reduce the communication gap between labor teams, procurement, and supervisors.
TYASuite Inventory Management, Zoho Inventory, and Odoo Inventory are a few inventory tracking software for construction.
The Techjockey team provides a free demo of these and a lot more inventory management software. You can try and wisely choose the software that meets your construction business needs.
Conclusion
Quote: A famous quote says, “Time is money”. But in construction, it goes as — “Labor’s productive time is money”. Skilled workers standing free, looking for unavailable materials, can result in project budget drains.
With construction inventory tracking software in use
- Companies can gain better visibility into construction resources.
- Materials arrive when needed.
- Tasks are completed on time.
- Labor is utilized efficiently.
All in all, by improving inventory tracking methods for construction projects, businesses can achieve higher profits.
FAQ
What is construction inventory management?
It is the process of dealing with material requirements on a construction site. It involves ordering, storing, distributing, and tracking all the resources.
What are the different types of construction inventory?
There are three types of inventories used in a construction business– building materials like cement, bricks, steel, etc. – Tools & equipment like hammers, welding machines, cranes, etc. – Consumables like cleaning supplies, water bottles, gloves, soap, lubricants, etc.
Mehlika Bathla is a passionate content writer who turns complex tech ideas into simple words. For over 4 years in the tech industry, she has crafted helpful content like technical documentation, user guides, UX content, website content, social media copies, and SEO-driven blogs. She is highly skilled in... Read more