Spare parts management is an essential function of any service workshop. Managing spares is a little complex process because of their comparatively smaller size and operating cost restraints. As a result, workshop owners are often hesitant to invest their time, money and efforts into handling spares and they find it as a cost-exhaustive function.
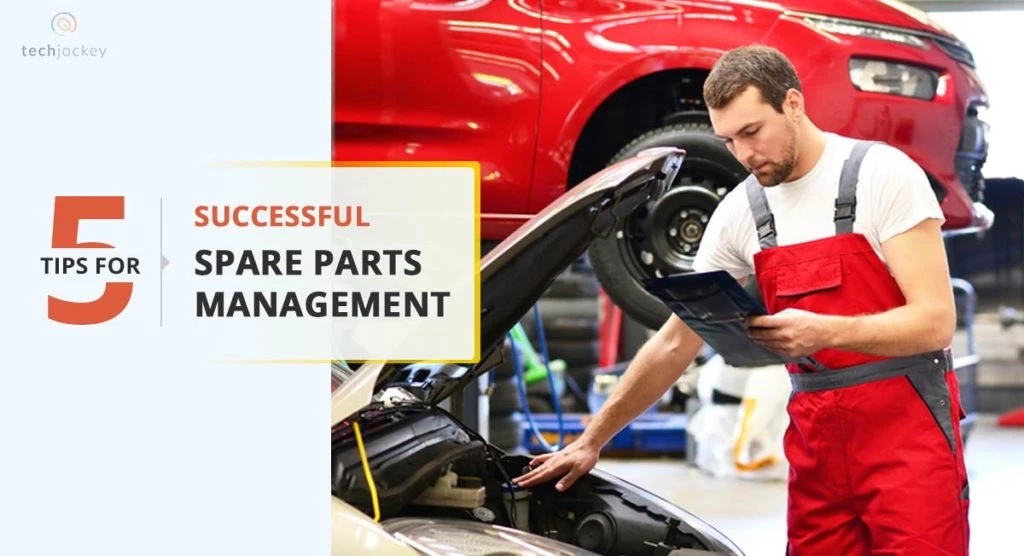
However, if a workshop foregoes spare parts management, it runs various risks like running out of stock and issuing faulty parts. All of which, eventually affects the bottom line.
5 Tips for Successful Spare Parts Management
- Have a Sound Operating Strategy
- Manage Your Spare Parts Inventory
- Understand Existing & Projected Consumption
- Shelf Life Management
- Identify Reliable Suppliers
So, what can you do to improve spare parts management in your workshop or garage? Well, here are five tips you can start with.
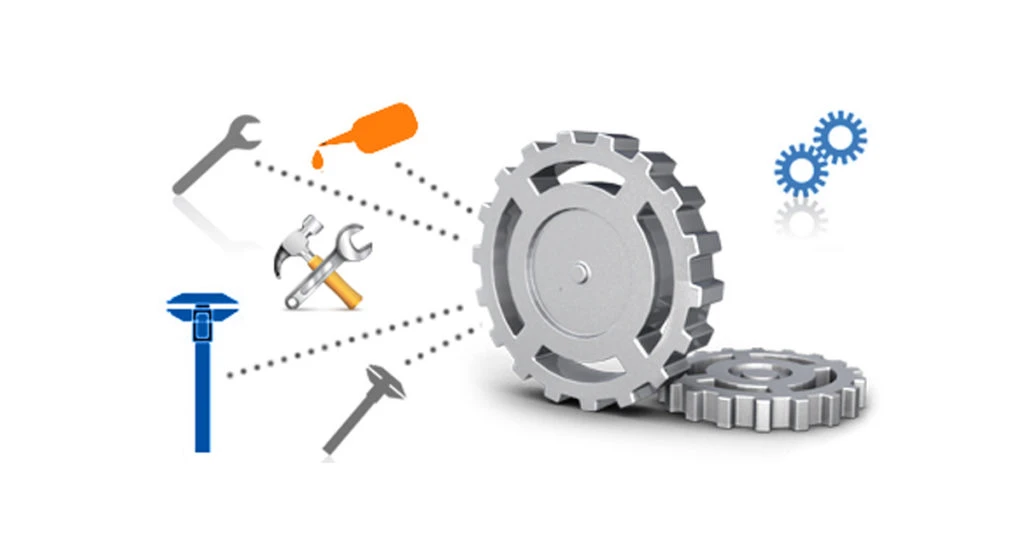
Have a Sound Operating Strategy
An operating strategy assists an organization with the allocation of resources in order to support infrastructure and production. Think of it like a blueprint for your spare management operation, detailing every nook and cranny and laying out plans for how to make it even better. With an operating strategy in place, your workshop can ensure better allocation and use of spare parts at minimum time and cost consumed. Having a sound operating strategy ensures that you’re armed against any unforeseen circumstance.
Operating strategy includes data collection and analysis, which helps you in the long run. For example, if optimal management of spare parts isn’t taking place, you can utilise the data collected to identify the reasons and quickly set counter-measures in place.
You can use a dealership management software like AutoBooom which comes with a dedicated spare parts management module. AutoBooom dealership management software allows you to create and store purchase orders of spare parts, maintain warranty information, scan and store parts information using barcode, and keep a complete track of their movement from storage to customer.
Manage Your Spare Parts Inventory
Inventory management is an essential function of any automobile-related function. Use techniques of inventory management to better stock products, for maximum consumption. Inventory management ensures that you’re sufficiently stocked (to prevent depleted/no stock) and allows you to analyse and identify the excess and the waste. Maximum space consumption at minimum effort and hassle is the ultimate purpose of inventory management.
When you manage your inventory properly, you can differentiate between the importance of different products and accordingly classify them. If there’s an excess of a particular spare part and comparatively less sale, you can take steps to clear out some of the excess in order to stock products with more demand
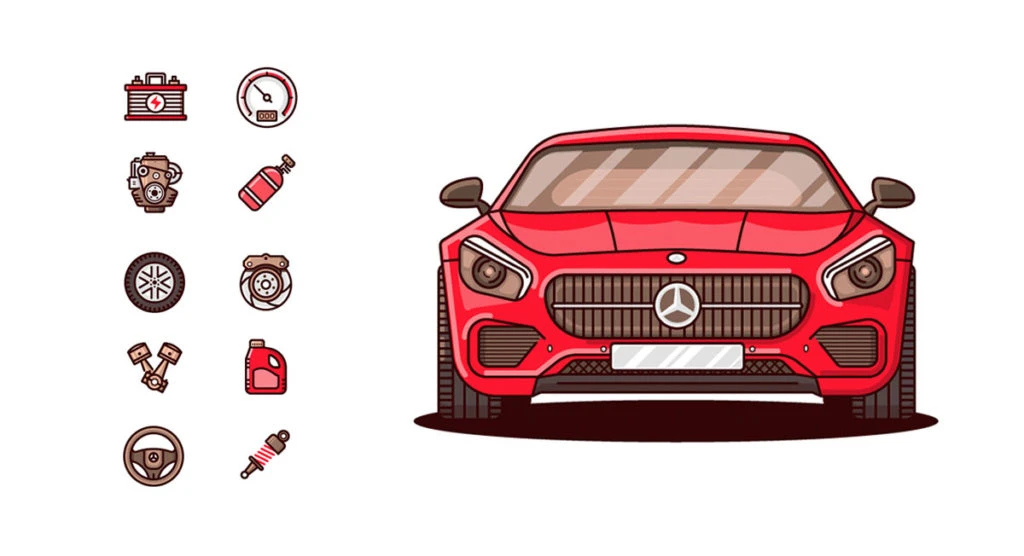
Understand Existing & Projected Consumption
Without a clear picture of your sale numbers and demand quotient, you will always face difficulty in successful spare parts management. You need to get into the habit of analysing your sale numbers to understand and predict future consumption. This will further assist you in managing your spare parts inventory, giving you the ability to order as per need, and prevent an excess or deficiency of spare parts stock.
Shelf Life Management
Spare parts, like everything else, have a limited shelf life. If that shelf life is exceeded and the part is used, it has the potential to impact reliability. Take a clutch wire for example. If a clutch wire is stored in a box and left unattended and uncared for years, the clutch wire could potentially rust and develop brittleness. If this wire is installed, how long will it last?
Spare parts also require maintenance. Take for example brake chains, which should be oiled on a periodic basis to prevent rusting and damage. If this is not done, the vehicle on which it is installed would be defected and lead to premature failure. The best way to make sure that your spares are preserved in the best possible way is to follow the manufacturer’s recommendations.
Identify Reliable Suppliers
When you use poor quality parts, they can result in failure, vehicle damage and more maintenance work. Identify quality-assured suppliers using a combination of maintenance records, sale records and consumer feedback. Procure from suppliers with good feedback who also fulfills your parts requirement. While corporate purchasing requirements might dictate your choice of suppliers, it is still possible to work with your purchasing department. You can use statistics and reports about vendor quality and reliability, to make your case.
While these aren’t very detailed, it gives you an idea of how to succeed in spare parts management for your workshop. Get into the habit of deploying these ideas and steadily but surely, your spare parts inventory won’t be a burden but an opportunity.
A self-confessed pop-culture enthusiast, he loves everything to do with movies, comic books and travelling. Studied at Christ University Bangalore with a triple major in Journalism, Psychology and English, he has been working as a technical content writer over the last few years. After pursuing MBA from T... Read more